Cechy ochronnej ochrony metalu przed korozją
Ochrona ochronna jest jedną z możliwych opcji ochrony materiałów konstrukcyjnych rurociągów przed korozją. Stosowany jest przede wszystkim na gazociągach i innych rurociągach.
Istota ochrony ochronnej
Ochroną ochronną jest zastosowanie specjalnej substancji - inhibitora, którym jest metal o podwyższonych właściwościach elektroujemnych. Pod wpływem powietrza ochraniacz rozpuszcza się, w wyniku czego metal nieszlachetny zostaje zatrzymany, pomimo wpływu czynników korozyjnych. Ochrona ochronna jest jedną z odmian katodowej metody elektrochemicznej.
Ta wersja powłok antykorozyjnych jest szczególnie często stosowana, gdy przedsiębiorstwo jest ograniczone zdolnością do zorganizowania ochrony katodowej przed procesami korozyjnymi o charakterze elektrochemicznym. Na przykład, jeśli możliwości finansowe lub technologiczne przedsiębiorstwa nie pozwalają na budowę linii energetycznych.
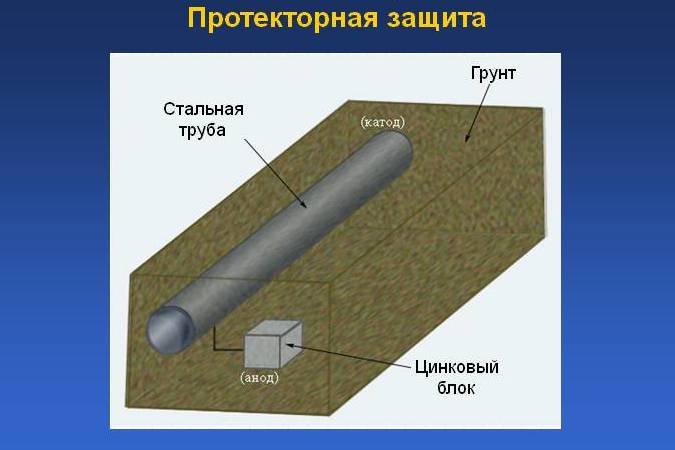
Ochrona inhibitora jest skuteczna, gdy rezystancja przejścia między chronionym obiektem a otaczającym go otoczeniem nie jest znacząca. Wysoka wydajność bieżnika jest możliwa tylko na pewnym dystansie. Do określenia tej odległości stosuje się definicję promienia antykorozyjnego zastosowanego bieżnika. Ta koncepcja pokazuje maksymalne usunięcie metalu ochronnego z chronionej powierzchni.
Istota procesów korozyjnych sprowadza się do tego, że najmniej aktywny metal w okresie oddziaływania przyciąga elektrony bardziej aktywnego metalu do własnych jonów. W ten sposób jednocześnie realizowane są dwa procesy:
- procesy redukcji w metalu o mniejszej aktywności (w katodzie);
- procesy utleniania metalu anodowego o minimalnej aktywności, dzięki którym rurociąg (lub inna konstrukcja stalowa) jest chroniony przed korozją.
Po pewnym czasie skuteczność ochraniacza spada (z powodu utraty kontaktu z chronionym metalem lub z powodu rozpuszczenia się składnika ochronnego). Z tego powodu konieczna jest wymiana bieżnika.
Cechy metody
Środki antykorozyjne w środowisku kwaśnym nie mają znaczenia. W takich środowiskach rozpuszczanie się bieżnika następuje w przyspieszonym tempie. Technikę zaleca się stosować wyłącznie w mediach neutralnych.
W porównaniu ze stalą bardziej aktywne są metale takie jak chrom, cynk, magnez, kadm i inne. Teoretycznie to właśnie te metale powinny być używane do ochrony rurociągów i innych konstrukcji metalowych. Istnieje jednak szereg cech, o których wiadomo, że można uzasadnić technologiczną bezsensowność stosowania czystych metali jako ochrony.
Na przykład magnez charakteryzuje się dużą szybkością rozwoju korozji, na aluminium szybko tworzy się gruba warstwa tlenku, a cynk dzięki specjalnej gruboziarnistej strukturze rozpuszcza się bardzo nierównomiernie. Aby zanegować takie negatywne właściwości czystych metali, dodaje się do nich pierwiastki stopowe. Innymi słowy, ochrona gazociągów i innych konstrukcji metalowych odbywa się przy użyciu wszelkiego rodzaju stopów.
Często stosuje się stopy magnezu. Oprócz głównego składnika - magnezu - zawierają aluminium (5-7%) i cynk (2-5%). Ponadto dodaje się niewielkie ilości niklu, miedzi i ołowiu. Stopy magnezu są odpowiednie do ochrony przed korozją w środowiskach, w których wartość pH nie przekracza 10,5 jednostki (tradycyjna gleba, świeże i lekko zasolone zbiorniki wodne). Ten ograniczający wskaźnik jest związany z szybkim rozpuszczaniem się magnezu na pierwszym etapie i dalszym pojawieniem się trudnych do rozpuszczenia związków.
Notatka! Stopy magnezu często prowadzą do pęknięć w wyrobach metalowych i zwiększają ich kruchość wodorową.
W przypadku konstrukcji metalowych znajdujących się w słonej wodzie (na przykład podwodny rurociąg podmorski) należy stosować zabezpieczenia na bazie cynku. Takie stopy zawierają również:
- aluminium (do 0,5%);
- kadm (do 0,15%);
- miedź i ołów (łącznie do 0,005%).
W środowisku słonej wody ochrona metali przed korozją za pomocą stopów cynku byłaby najlepszą opcją. Jednak w zbiornikach słodkowodnych i na zwykłej glebie takie osłony bardzo szybko zarastają tlenkami i wodorotlenkami, w wyniku czego środki antykorozyjne tracą sens.
Protektory cynkowe coraz częściej stosowane są do ochrony przed korozją tych konstrukcji metalowych, w których warunki technologiczne wymagają najwyższego stopnia bezpieczeństwa przeciwpożarowego i przeciwwybuchowego. Przykładem zapotrzebowania na takie stopy są gazociągi i rurociągi do transportu cieczy palnych.
Ponadto związki cynku nie tworzą zanieczyszczeń w wyniku rozpuszczania anodowego. Dlatego takie stopy są praktycznie bezsporne, gdy konieczne jest zabezpieczenie rurociągu do transportu konstrukcji naftowych lub metalowych na tankowcach.
W warunkach słonej wody płynącej na szelfie przybrzeżnym często stosuje się stopy aluminium. Takie kompozycje zawierają kadm, tal, ind, krzem (łącznie do 0,02%), a także magnez (do 5%) i cynk (do 8%). Właściwości bieżnika mieszanek aluminium są zbliżone do właściwości stopów magnezu.
Kombinacja protektorów i farb
Często konieczne jest zabezpieczenie gazociągu przed korozją nie tylko protektorem, ale również materiałem do malowania i lakierowania. Farba jest uważana za pasywną metodę ochrony przed procesami korozyjnymi i jest naprawdę skuteczna tylko w połączeniu z zastosowaniem protektora.
Ta technika łączenia pozwala:
- Zmniejszenie negatywnego wpływu potencjalnych wad w powłokach konstrukcji metalowych (łuszczenie, pęcznienie, pękanie, pęcznienie itp.). Takie wady istnieją nie tylko w wyniku wad fabrycznych, ale także w związku z czynnikami naturalnymi.
- Zmniejszają (czasem bardzo znaczną ilość) zużycie drogich ochraniaczy, jednocześnie wydłużając ich żywotność.
- Aby bardziej równomiernie rozprowadzić warstwę ochronną na metalu.
Warto również zauważyć, że kompozycje farb i lakierów są często trudne do nałożenia na niektóre powierzchnie już działającego gazociągu, cysterny lub innej konstrukcji metalowej. W takich przypadkach wystarczy zrezygnować z ochraniacza ochronnego.