Rodzaje kołnierzy
Kołnierz to sposób łączenia rur, zaworów, pomp i innych urządzeń w system rurociągów. Ta metoda połączenia zapewnia łatwy dostęp w celu czyszczenia, kontroli lub modyfikacji. Kołnierze są zwykle gwintowane lub spawane. Połączenie kołnierzowe składa się z dwóch kołnierzy skręcanych śrubami oraz uszczelki między nimi zapewniającej szczelność.
Kołnierze rurowe są wykonane z różnych materiałów. Kołnierze są obrabiane powierzchniowo, z żeliwa szarego i sferoidalnego, ale najczęściej stosowanym materiałem jest kuta stal węglowa.
Najczęściej używane kołnierze w przemyśle naftowym i chemicznym:
- z szyjką do spawania
- przez kołnierz
- spawane z wgłębieniem do wspawania
- spawana zakładka (swobodnie obracająca się)
- gwintowany kołnierz
- korek kołnierzowy
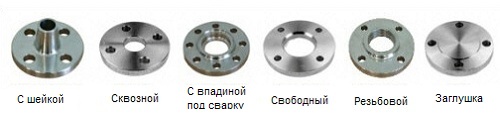
Wszystkie typy kołnierzy, z wyjątkiem wolnych, mają wzmocnioną powierzchnię.
Kołnierze specjalne
Z wyjątkiem kołnierzy wymienionych powyżej, istnieje szereg kołnierzy specjalnych, takich jak:
- kołnierz membranowy
- długie przyspawane kołnierze kołnierzowe
- kołnierz rozprężny
- kołnierz adaptera
- korek oczkowy (część połączenia kołnierzowego)
- korki talerzowe i pierścienie pośrednie (część połączenia kołnierzowego)
Najpopularniejszymi materiałami używanymi na kołnierze są stal węglowa, stal nierdzewna, żeliwo, aluminium, mosiądz, brąz, plastik itp. Ponadto kołnierze, podobnie jak kształtki i rury do zastosowań specjalnych, są czasami pokryte od wewnątrz warstwą materiału o zupełnie innej jakości niż same kołnierze. Są to kołnierze wyłożone. Materiał kołnierzy jest najczęściej ustalany przy doborze rur. Z reguły kołnierz jest wykonany z tego samego materiału, co same rury.
Przykład kołnierza do przyspawania kołnierza 6" — 150#-S40
Każdy kołnierz ASME B16.5 ma kilka standardowych rozmiarów. Jeśli projektant w Japonii, osoba przygotowująca projekt do rozruchu w Kanadzie lub monter rurociągów w Australii mówi o kołnierzu spawalniczym 6"-150#-S40 wg ASME B16.5, to ma na myśli kołnierz, który pokazano poniżej.
W przypadku zamówienia kołnierza dostawca chciałby poznać jakość materiału. Na przykład ASTM A105 jest tłoczonym kołnierzem ze stali węglowej, podczas gdy A182 jest tłoczonym kołnierzem ze stali stopowej. W związku z tym, zgodnie z przepisami, obie normy muszą być określone dla dostawcy: Weld Flange 6"-150#-S40-ASME B16.5/ASTM A105.
KLASA CIŚNIENIA
Klasa ciśnienia lub ocena dla kołnierzy będzie wyrażona w funtach. Do określenia klasy ciśnienia używane są różne nazwy. Na przykład: 150 funtów lub 150 funtów lub 150# lub klasa 150 oznaczają to samo.
Kołnierze ze stali kutej mają 7 głównych klasyfikacji:
150 funtów - 300 funtów - 400 funtów - 600 funtów - 900 funtów - 1500 funtów - 2500 funtów
Pojęcie klasyfikacji kołnierzy jest jasne i oczywiste. Kołnierz klasy 300 może wytrzymać wyższe ciśnienia niż kołnierz klasy 150, ponieważ kołnierz klasy 300 ma więcej metalu i może wytrzymać wyższe ciśnienia. Istnieje jednak szereg czynników, które mogą wpływać na limit ciśnienia kołnierza.
PRZYKŁAD
Kołnierze mogą wytrzymać różne ciśnienia w różnych temperaturach. Wraz ze wzrostem temperatury spada klasa ciśnienia kołnierza. Na przykład, kołnierz Class 150 jest oceniany na około 270 PSIG przy temperaturze otoczenia, 180 PSIG przy 200 ° C, 150 PSIG przy 315°C i 75 PSIG przy 426 ° C.
Dodatkowym czynnikiem jest to, że kołnierze mogą być wykonane z różnych materiałów, takich jak stal stopowa, żeliwo, żeliwo sferoidalne itp. Każdy materiał ma różne klasy ciśnienia.
PARAMETR „CIŚNIENIE-TEMPERATURA”
Klasa ciśnieniowo-temperaturowa określa robocze, maksymalne dopuszczalne nadciśnienie w barach w temperaturze w stopniach Celsjusza. W przypadku temperatur pośrednich dozwolona jest interpolacja liniowa. Interpolacja między klasami notacji nie jest dozwolona.
Klasyfikacje temperaturowo-ciśnieniowe
Klasa temperatura-ciśnienie ma zastosowanie do połączeń kołnierzowych, które są zgodne z ograniczeniami dotyczącymi połączeń śrubowych i uszczelek wykonanych zgodnie z dobrą praktyką montażu i wyrównania. Za zastosowanie tych klas do połączeń kołnierzowych, które nie spełniają tych ograniczeń, odpowiada użytkownik.
Temperatura pokazana dla odpowiedniej klasy ciśnienia jest temperaturą wewnętrznej powłoki części. Zasadniczo ta temperatura jest taka sama jak zawartej cieczy. Zgodnie z wymaganiami obowiązujących norm i przepisów, w przypadku stosowania klasy ciśnienia odpowiadającej temperaturze innej niż przepływająca ciecz, cała odpowiedzialność spoczywa na kliencie. Dla jakiejkolwiek temperatury poniżej -29°C, ocena nie może być wyższa niż przy temperaturze -29°C.
Jako przykład poniżej znajdują się dwie tabele z grupami materiałów zgodnie z ASTM oraz dwie inne tabele z klasą temperaturowo-ciśnieniową dla tych materiałów zgodnie z ASME B16.5.
Materiały ASTM grupa 2-1.1 |
|||
Oznaczenie nominalne |
Cechowanie |
Odlew |
talerze |
C-Si | A105(1) | A216 Gr.WCB(1) |
A515 Gr.70(1) |
C-Mn-Si | A350 Gr.LF2(1) | - | A516 Gr.70(1),(2) |
C-Mn-Si-V | A350 Gr.LF6 Cl 1(3) | - | A537 kl.1(4) |
3½ Ni |
A350 Gr.LF3 |
- | - |
UWAGI:
|
Klasa temperatury i ciśnienia dla materiałów grupy ASTM 2.1.1 Ciśnienie robocze według klasy |
|||||||
Temperatura °C | 150 | 300 |
400 |
600 |
900 |
1500 |
2500 |
od 29 do 38 |
19.6 | 51.1 | 68.1 | 102.1 | 153.2 | 255.3 | 425.5 |
50 | 19.2 | 50.1 | 66.8 | 100.2 | 150.4 | 250.6 | 417.7 |
100 | 17.7 | 46.6 | 62.1 | 93.2 | 139.8 | 233 | 388.3 |
150 | 15.8 | 45.1 | 60.1 | 90.2 | 135.2 | 225.4 | 375.6 |
200 | 13.8 | 43.8 | 58.4 | 87.6 | 131.4 | 219 | 365 |
250 | 12.1 | 41.9 | 55.9 | 83.9 | 125.8 | 209.7 | 349.5 |
300 | 10.2 | 39.8 | 53.1 | 79.6 | 119.5 | 199.1 | 331.8 |
325 | 9.3 | 38.7 | 51.6 | 77.4 | 116.1 | 193.6 | 322.6 |
350 | 8.4 | 37.6 | 50.1 | 75.1 | 112.7 | 187.8 | 313 |
375 | 7.4 | 36.4 | 48.5 | 72.7 | 109.1 | 181.8 | 303.1 |
400 | 6.5 | 34.7 | 46.3 | 69.4 | 104.2 | 173.6 | 289.3 |
425 | 5.5 | 28.8 | 38.4 | 57.5 | 86.3 | 143.8 | 239.7 |
450 | 4.6 | 23 | 30.7 | 46 | 69 | 115 | 191.7 |
475 | 3.7 | 17.4 | 23.2 | 34.9 | 52.3 | 87.2 | 145.3 |
500 | 2.8 | 11.8 | 15.7 | 23.5 | 35.3 | 58.8 | 97.9 |
538 | 1.4 | 5.9 | 7.9 | 11.8 | 17.7 | 29.5 | 49.2 |
Klasa temperatury i ciśnienia dla materiałów grupy ASTM 2-2.3 Ciśnienie robocze według klasy |
|||||||
Temperatura °C | 150 | 300 |
400 |
600 |
900 |
1500 |
2500 |
od 29 do 38 |
15.9 |
41.4 |
55.2 |
82.7 |
124.1 |
206.8 |
344.7 |
50 | 15.3 |
40 |
53.4 |
80 |
120.1 |
200.1 |
333.5 |
100 | 13.3 |
34.8 |
46.4 |
69.6 |
104.4 |
173.9 |
289.9 |
150 | 12 |
31.4 |
41.9 |
62.8 |
94.2 |
157 |
261.6 |
200 | 11.2 |
29.2 |
38.9 |
58.3 |
87.5 |
145.8 |
243 |
250 | 10.5 |
27.5 |
36.6 |
54.9 |
82.4 |
137.3 |
228.9 |
300 | 10 |
26.1 |
34.8 |
52.1 |
78.2 |
130.3 |
217.2 |
325 | 9.3 |
25.5 |
34 |
51 |
76.4 |
127.4 |
212.3 |
350 | 8.4 |
25.1 |
33.4 |
50.1 |
75.2 |
125.4 |
208.9 |
375 | 7.4 |
24.8 |
33 |
49.5 |
74.3 |
123.8 |
206.3 |
400 | 6.5 |
24.3 |
32.4 |
48.6 |
72.9 |
121.5 |
202.5 |
425 | 5.5 |
23.9 |
31.8 |
47.7 |
71.6 |
119.3 |
198.8 |
450 | 4.6 |
23.4 |
31.2 |
46.8 |
70.2 | 117.1 |
195.1 |
POWIERZCHNIA KOŁNIERZA
Kształt i konstrukcja powierzchni kołnierza determinuje położenie pierścienia uszczelniającego lub uszczelki.
Najczęściej używane typy:
- podniesiona powierzchnia (RF)
- płaska powierzchnia (FF)
- rowek na oring (RTJ)
- z gwintem męskim i żeńskim (M&F)
- pióro i wpust (T&G)
Podniesiona powierzchnia czołowa, najbardziej odpowiedni typ kołnierza, łatwy do zidentyfikowania. Ten typ jest tak nazywany, ponieważ powierzchnia uszczelki wystaje ponad powierzchnię połączenia śrubowego.
Średnica i wysokość są definiowane zgodnie z ASME B16.5 przy użyciu klasy ciśnienia i średnicy. W klasie ciśnienia do 300 Lbs wysokość wynosi około 1,6 mm, a w klasie ciśnienia od 400 do 2500 Lbs wysokość wynosi około 6,4 mm. Klasa ciśnienia kołnierza określa wysokość podniesionej powierzchni. Celem kołnierza (RF) jest skoncentrowanie większego nacisku na mniejszej powierzchni uszczelki, zwiększając w ten sposób granicę ciśnienia złącza.
Dla parametrów wysokości wszystkich kołnierzy opisanych w tym artykule stosuje się wymiary H i B, z wyjątkiem kołnierza złącza zakładkowego, należy to rozumieć i pamiętać w następujący sposób:
W klasach ciśnienia 150 i 300 funtów wysokość występu wynosi około 1,6 mm (1/16 cala). Prawie wszyscy dostawcy kołnierzy w tych dwóch klasach podają wymiary H i B w swoich broszurach lub katalogach, łącznie z powierzchnią czołową (patrz Rys.1 poniżej)
W klasach ciśnienia 400, 600, 900, 1500 i 2500 funtów wysokość występu wynosi 1/4 cala (6,4 mm). W tych klasach wielu dostawców podaje wymiary H i B, nie uwzględniając wysokości występu (patrz Rys.2 powyżej)
W tym artykule znajdziesz dwa rozmiary. Górny wiersz wymiarów nie obejmuje wysokości występu, a wymiary w dolnym wierszu uwzględniają wysokość występu.
PŁASKA POWIERZCHNIA (FF — płaska powierzchnia)
W przypadku kołnierza z płaską powierzchnią (pełną) uszczelka znajduje się w tej samej płaszczyźnie co połączenie śrubowe. Najczęściej kołnierze z płaską powierzchnią czołową są używane tam, gdzie odlewany jest kołnierz współpracujący lub złączka.
Kołnierz o płaskiej powierzchni nigdy nie łączy się z kołnierzem podniesionym. Zgodnie z ASME B31.1, przy łączeniu płaskich kołnierzy żeliwnych z kołnierzami ze stali węglowej należy usunąć występ na kołnierzu stalowym i uszczelnić całą powierzchnię uszczelką. Ma to na celu ochronę cienkiego, kruchego kołnierza żeliwnego przed pękaniem z powodu wystawania kołnierza stalowego.
KOŁNIERZ Z KOŃCÓWKĄ DO USZCZELKI O-RING (RTJ - Ring Type Joint)
Kołnierze RTJ mają wycięte na powierzchni rowki, w które wkładane są stalowe oringi. Kołnierze są uszczelnione, ponieważ podczas dokręcania śrub uszczelka między kołnierzami jest wciskana w rowki, odkształcana, tworząc bliski kontakt metal-metal.
Kołnierz RTJ może mieć wargę z wykonanym w nim pierścieniowym rowkiem. Ten występ nie służy jako żadna pieczęć. W przypadku kołnierzy RTJ, które są uszczelnione za pomocą O-ringów, podniesione powierzchnie współpracujących i dokręconych kołnierzy mogą stykać się ze sobą. W takim przypadku ściśnięta uszczelka nie będzie już przenosić dodatkowych obciążeń, dokręcanie śrub, wibracje i przemieszczenie nie będą już powodować zgniatania uszczelki i zmniejszania siły dokręcania.
Metalowe oringi nadają się do stosowania w wysokich temperaturach i ciśnieniach. Wykonane są z odpowiedniego doboru materiału i profilu i zawsze są stosowane w odpowiednich kołnierzach, zapewniając dobre i niezawodne uszczelnienie.
Pierścienie O-ring są zaprojektowane tak, aby uszczelnienie było osiągane przez „wprowadzającą linię styku” lub klinowanie pomiędzy kołnierzem współpracującym a uszczelką. Poprzez wywieranie nacisku na uszczelkę przez śruby, bardziej miękki metal uszczelki wnika w delikatną strukturę sztywniejszego materiału kołnierza i tworzy bardzo szczelne i skuteczne uszczelnienie.
Najczęściej używane pierścienie:
Typ R-Owal zgodnie z ASME B16.20
Nadaje się do kołnierzy ASME B16.5 o klasie ciśnieniowej 150 do 2500.
Typ R-Ośmiokątny zgodnie z ASME 16.20
Ulepszony projekt w stosunku do oryginalnego R-Oval. Można ich jednak używać tylko do płaskich kołnierzy z rowkiem. Nadaje się do kołnierzy ASME B16.5 o klasie ciśnieniowej 15 do 2500.
KOŁNIERZE Z USZCZELNIENIEM I POWIERZCHNIOWYM LUG-VESSEL (LMF - Duża męska twarz; LFF - Duża żeńska twarz)
Kołnierze tego typu muszą pasować. Jedna powierzchnia kołnierza ma obszar, który rozciąga się poza normalne granice powierzchni kołnierza ( tata). Drugi kołnierz lub przeciwkołnierz ma odpowiednie wgłębienie ( Mama) wykonane na jego powierzchni.
Układanie półluźne
- Głębokość podcięcia (karbu) jest zwykle równa lub mniejsza niż wysokość występu, aby zapobiec kontaktowi metalu z metalem, gdy uszczelka jest ściskana
- Głębokość nacięcia jest zwykle nie większa niż 1/16 cala większa niż wysokość wargi
KOŁNIERZ Z POWIERZCHNIĄ USZCZELNIAJĄCĄ
(Protruzja – język języka – TF; zagłębienie – twarz rowka – GF)
Kołnierze tego typu również muszą pasować. Jeden kołnierz ma pierścień z występem (cierniem) wykonanym na powierzchni tego kołnierza, podczas gdy rowek jest obrabiany na powierzchni odpowiednika. Takie powierzchnie są powszechnie spotykane na pokrywach pomp i pokrywach zaworów.
Naprawiono uszczelkę
- Wymiary uszczelki są takie same lub mniejsze niż wysokość rowka
- Uszczelka szersza niż rowek nie większa niż 1/16"
- Wymiary uszczelki będą dopasowane do wymiarów rowka
- Podczas demontażu połączenie należy rozpiąć osobno
PŁASKA POWIERZCHNIA I ROWKI
Naprawiono uszczelkę
- Jedna powierzchnia jest płaska, druga jest karbowana
- Do zastosowań, w których wymagana jest precyzyjna kontrola docisku uszczelki
- Zalecane są tylko uszczelki sprężyste - spiralne, z wydrążonym pierścieniem, uruchamiane ciśnieniem i z metalową osłoną
WYKOŃCZENIE POWIERZCHNI KOŁNIERZ
ASME B16.5 wymaga, aby powierzchnia kołnierza (powierzchnia podniesiona i powierzchnia płaska) miała pewną chropowatość, aby ta powierzchnia, po wyrównaniu z uszczelką, zapewniała dobre uszczelnienie.
Ostateczne rowkowanie, koncentryczne lub spiralne, wymaga od 30 do 55 rowków na cal, co daje chropowatość między 125 a 500 mikrocalami. Umożliwi to producentom kołnierzy przetwarzanie dowolnej klasy metalowych uszczelek kołnierzowych.
W rurociągach transportujących substancje grupy A i B obiektów technologicznych I kategorii wybuchowości nie wolno stosować połączeń kołnierzowych o gładkiej powierzchni uszczelniającej, z wyjątkiem przypadków stosowania uszczelek spiralnie zwijanych.
NAJCZĘŚCIEJ UŻYWANE POWIERZCHNIE
Zgrubna
Najczęściej stosowany w obróbce dowolnego kołnierza, ponieważ nadaje się do prawie wszystkich typowych warunków pracy. Po ściśnięciu miękka powierzchnia uszczelki będzie stykać się z obrabianą powierzchnią, co pomoże stworzyć uszczelnienie, a między połączonymi częściami wystąpi wysoki poziom tarcia. Wykańczanie tych kołnierzy odbywa się za pomocą frezu o promieniu 1,6 mm z posuwem 0,88 mm na obrót dla 12 cali. W przypadku 14 cali i większych obróbka odbywa się za pomocą frezu o promieniu 3,2 mm z posuwem 1,2 mm na odwrót. |
![]() |
![]() |
Spiralne wycięcie
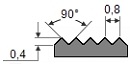
Koncentryczne nacięcie.Jak sama nazwa wskazuje, obróbka składa się z koncentrycznych rowków. Stosuje się nóż 90°, a pierścienie są równomiernie rozłożone na całej powierzchni.
Gładka powierzchnia.Takie przetwarzanie nie pozostawia wizualnie śladów narzędzia. Takie powierzchnie są zwykle używane do uszczelek z metalową powierzchnią, takich jak podwójna osłona, płaska stal lub blacha falista. Gładka powierzchnia pomaga stworzyć uszczelnienie i zależy od płaskości przeciwległej powierzchni. Zazwyczaj osiąga się to dzięki powierzchni styku uszczelki utworzonej przez ciągły (czasami nazywany fonograficznym) spiralny rowek wykonany za pomocą frezu o promieniu 0,8 mm, przy prędkości posuwu 0,3 mm na obrót, o głębokości 0,05 mm. Spowoduje to chropowatość między Ra 3,2 a 6,3 mikrometra (125-250 mikro cali)
USZCZELKI
Do wykonania szczelnego połączenia kołnierzowego potrzebne są uszczelki.
Uszczelka to skompresowane arkusze lub pierścienie służące do tworzenia wodoodpornego połączenia między dwiema powierzchniami. Uszczelki są produkowane tak, aby wytrzymać ekstremalne temperatury i ciśnienia i są dostępne z materiałów metalowych, półmetalicznych i niemetalicznych.
Na przykład zasada uszczelnienia może polegać na ściśnięciu uszczelki między dwoma kołnierzami. Uszczelka wypełnia mikroskopijne przestrzenie i nierówności powierzchni kołnierzy, a następnie tworzy uszczelnienie, które zapobiega wyciekom cieczy i gazów. Wymagana jest prawidłowa i staranna instalacja uszczelki, aby zapobiec wyciekom w połączeniu kołnierzowym.
Ten artykuł opisuje uszczelki zgodne z ASME B16.20 (metalowe i półmetalowe uszczelki kołnierzy do rur) i ASME B16.21 (niemetalowe uszczelki do płaskich rur)
ŚRUBY
Do połączenia dwóch kołnierzy wymagane są śruby. Liczba będzie określona przez liczbę otworów w kołnierzu, a średnica i długość śrub będzie zależeć od rodzaju kołnierza i jego klasy ciśnieniowej. Najczęściej stosowanymi śrubami w przemyśle naftowym i chemicznym do kołnierzy ASME B16.5 są śruby dwustronne. Kołek składa się z pręta gwintowanego i dwóch nakrętek. Innym dostępnym rodzajem śruby jest zwykła śruba sześciokątna z jedną nakrętką.
Wymiary, tolerancje wymiarowe itp. zostały zdefiniowane w ASME B16.5 i ASME B18.2.2, materiały w różnych normach ASTM.
MOMENT OBROTOWY
Aby uzyskać szczelne połączenie kołnierzowe, uszczelka musi być prawidłowo zamontowana, śruby muszą mieć właściwy moment dokręcania, a całkowite naprężenie dokręcania musi być równomiernie rozłożone na całym kołnierzu.
Niezbędne rozciąganie odbywa się dzięki momentowi dokręcania (napięcie wstępne na element złączny poprzez przekręcenie jego nakrętki).
Prawidłowy moment dokręcania śruby pozwala na najlepsze wykorzystanie jej właściwości elastycznych. Aby dobrze wykonywać swoją pracę, śruba musi zachowywać się jak sprężyna. Podczas pracy proces dokręcania powoduje osiowe naprężenie wstępne śruby. Oczywiście ta siła rozciągająca jest równa przeciwstawnym siłom ściskającym przykładanym do elementów zespołu. Może być określany jako siła dokręcania lub siła rozciągająca.
KLUCZ DYNAMOMETRYCZNY
Klucz dynamometryczny to ogólna nazwa narzędzia ręcznego, które służy do przykładania precyzyjnego momentu obrotowego do złącza, niezależnie od tego, czy jest to śruba, czy nakrętka. Pozwala to operatorowi zmierzyć siłę obrotową (moment obrotowy) przyłożoną do śruby, która musi być zgodna ze specyfikacją.
Wybór odpowiedniej techniki dokręcania śrub kołnierza wymaga doświadczenia. Prawidłowe zastosowanie którejkolwiek z technik wymaga również kwalifikacji zarówno narzędzia, które ma być użyte, jak i specjalisty, który będzie wykonywał pracę. Poniżej znajdują się najczęściej stosowane metody dokręcania śrub:
- dokręcanie ręcznie
- klucz pneumatyczny
- hydrauliczny klucz dynamometryczny
- ręczny klucz dynamometryczny z wahaczem lub przekładnią
- hydrauliczny napinacz śrub
Strata momentu obrotowego jest nieodłącznym elementem każdego połączenia śrubowego. Połączony efekt poluzowania śrub (około 10% w ciągu pierwszych 24 godzin po montażu), pełzanie uszczelki, wibracje w systemie, rozszerzalność cieplna i elastyczne oddziaływanie podczas dokręcania śrub przyczyniają się do utraty momentu obrotowego. Kiedy utrata momentu obrotowego osiąga poziom krytyczny, ciśnienie wewnętrzne przekracza siłę ściskającą, która utrzymuje uszczelkę na miejscu, w którym to przypadku może wystąpić wyciek lub rozerwanie.
Kluczem do ograniczenia tych efektów jest właściwe umieszczenie uszczelek. Podczas montażu uszczelki konieczne jest połączenie kołnierzy i płynne i równoległe dokręcanie, przy najmniejszym momencie dokręcania, 4 śruby, zgodnie z prawidłową kolejnością dokręcania. Zmniejszy to koszty operacyjne i poprawi bezpieczeństwo.
Ważna jest również prawidłowa grubość uszczelki. Im grubsza uszczelka, tym większe jej pełzanie, co z kolei może prowadzić do utraty momentu dokręcania. Norma ASME dla ząbkowanych kołnierzy generalnie zaleca uszczelkę 1,6 mm. Cieńsze materiały mogą działać przy wyższych obciążeniach uszczelek, a tym samym wyższych ciśnieniach wewnętrznych.
SMAROWANIE ZMNIEJSZA TARCIE
Smarowanie zmniejsza tarcie podczas dokręcania, zmniejsza zrzucanie śrub podczas instalacji i zwiększa żywotność. Zmiana współczynnika tarcia wpływa na wielkość napięcia wstępnego osiąganego przy danym momencie dokręcania. Większy współczynnik tarcia skutkuje mniejszą konwersją momentu obrotowego na napięcie wstępne. Wartość współczynnika tarcia podana przez producenta smaru musi być znana, aby dokładnie ustawić wymaganą wartość momentu obrotowego.
Smar lub środki zapobiegające zacieraniu muszą być nałożone zarówno na powierzchnię nakrętki łożyska, jak i na gwint zewnętrzny.
KOLEJNOŚĆ DOKRĘCANIAW pierwszym przejściu lekko dokręć pierwszą śrubę, następnie następną naprzeciw niej, następnie ćwierć obrotu po okręgu (lub 90 stopni), aby dokręcić trzecią śrubę, a naprzeciw niej czwartą. Kontynuuj tę sekwencję, aż wszystkie śruby zostaną dokręcone. Podczas dokręcania kołnierzy z czterema śrubami należy stosować wzór krzyżowy.
PRZYGOTOWANIE DO MOCOWANIA KOŁNIERZA
W celu uzyskania szczelności w połączeniach kołnierzowych konieczne jest, aby wszystkie elementy były dokładne.
Przed rozpoczęciem procesu łączenia należy wykonać następujące kroki, aby uniknąć problemów w przyszłości:
- Oczyść powierzchnie kołnierzy i sprawdź, czy nie ma zarysowań, powierzchnie muszą być czyste i wolne od wszelkich wad (wybojów, wgłębień, wgnieceń itp.)
- Sprawdź wszystkie śruby i nakrętki pod kątem uszkodzeń lub korozji gwintów. W razie potrzeby wymień lub napraw śruby lub nakrętki
- Usuń zadziory ze wszystkich wątków
- Nasmaruj gwinty śrub lub kołków oraz powierzchnie nakrętek przylegające do kołnierza lub podkładki. W większości zastosowań zalecane są podkładki hartowane.
- Zainstaluj nową uszczelkę i upewnij się, że jest wyśrodkowana. NIE UŻYWAJ STAREJ USZCZELKI ani nie używaj wielu uszczelek.
- Sprawdź wyrównanie kołnierza zgodnie ze standardem rurociągów procesowych ASME B31.3
- Wyreguluj położenie nakrętek, aby upewnić się, że 2-3 gwinty znajdują się powyżej górnej części gwintu.